Use Case
Roasting Industry
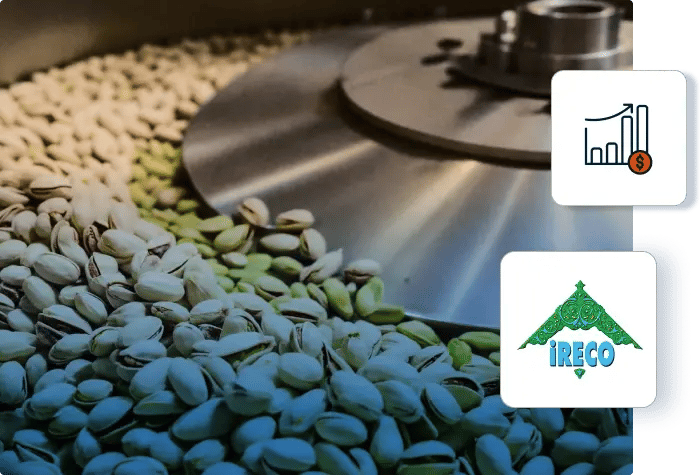
Industry/ Roasting
Functionalities
#digital-twin #process-optimization #energy-efficiency
Optimizing Pistachio Roasting for Humidity Precision and Efficiency
Ireco, a leading producer of pistachios, aimed to improve their roasting process by achieving a consistent target humidity in their final product. Their goals included minimizing energy consumption, managing the natural variability in raw material properties and improving machinery reliability to achieve stable quality.
Challenge
The priority in the roasting industry are to achieve the target humidity in the end product, use the least amount of energy to do so and keep quality consistent. The difficulty lies is the variability of humidity in the raw product and the amount of energy used to achieve the desired level of roasting.
Wizata partnered with Ireco to develop and implement a recommendation system designed to optimize their roasting process in two steps:
➜ Real-Time Setpoint Recommendation
Develop a model that dynamically calculates optimal process parameters for three specific setpoints to achieve the desired final humidity depending on the raw material characteristics. The system needed to account for the natural variability of raw material humidity and the unpredictable humidity loss during roasting and packing.
➜ Data-Driven Automation
Set up automated adjustments to roasting conditions based on predictive insights, ensuring process a quality consistency consistency. Adjusting the setpoint in an automated way has the objective of further optimizing energy consumption.
Approach
Wizata and the local experts worked closely to ensure that the project generated measurable ROI and business impact.
The following activities were performed:
➜ Set up of Wizata platform, hosted within customers’ Azure tenant
➜ Ingest metadata from the roaster sensors, the raw material and the end product
➜ Design and build a Centric Digital Twin based upon the roaster used
➜ Transform and contextualize process data
➜ Use an specific ML models of the platform and produce real-time recommendations
➜ Build customized dashboards for relevant stakeholders
➜ Replicate the model in two additional roasters
Outcome
The implementation brought measurable improvements across critical aspects of Ireco’s operations:
➜ Energy Efficiency: The project led to a tangible 3% reduction in energy consumption. This improvement lowered operational costs and aligned with Ireco’s commitment to sustainable practices.
➜ Increased Output: Improved process consistency and achieving the desired humidity level contributed to a boost in annual production value, representing a return on investment that quadrupled the initial expenditure in one year.
➜ The contextualized data within Wizata now allows for quick responses to incidents in real-time to prevent deviations from desired quality and improve reliability.
➜ The models are maintained in a centralized way allowing them to easily implement changes for all their roasters in no time.
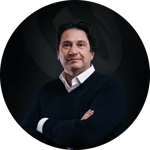
Get in touch with one of our experts
Philippe Maes
pma@wizata.com
+32 476 209 149