Use Case
Process Manufacturing
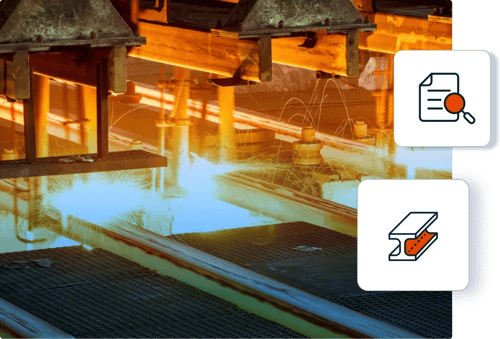
Industry/ Process Manufacturing
Functionalities
#machine-learning #automation #process-optimization
Process automation as scalable prototype
In its constant effort to leverage digitalization and industry 4.0 loT, a global lime producer has the goal of automating Kiln, a furnace technology, within their plants in several locations and optimizing their daily operations with the use of data-driven insights from production data. As a result of the combined efforts between the client and Wizata, there are currently 10 kilns in different continents that are running autonomously with limited human intervention, producing higher quality, and guaranteeing highest asset availability with associated reduced stoppages and maintenance costs.
Challenge
The current system based on empirical and mathematical formulas does not provide flexibility and adaptability. The goal is to use smart systems that can support and even execute autonomous decisions, improving existing production processes. Through the Wizata platform, the client established a system that optimizes everyday operations, is scalable and replicable throughout their global sites, and focuses on the following processes:
➜ Data-driven setpoints automation, stabilizing the process, and maximizing energy and quality efficiencies
➜ Anomaly detection system anticipating potential failures allowing maintenance scheduling tasks only on misbehaving equipment
Approach
All existing data processing systems are transferred to a cloud-based architecture to guarantee scalability and facilitate access to multiple data sources.
Variables with a major influence on process stability are identified through data exploration and machine learning models on consolidated data.
Control algorithms are built to ensure the process delivers target quality and system stability. In addition, the anomaly detection system instantly alerts the operation teams to restore production processes' full capacity and efficiency.
Outcome
The combination of both solutions has led to measurable improvements to main production KPls like:
Process stability
➜ Reduction of overall energy consumption (-3% solid fuel consumption)
➜ Quality stabilized around optimal targets (+10% increase of top quality, -70% decrease of unsold inferior quality)
➜ Long-term improvement and stabilization of asset reliability
Anomaly detection
➜ Faster root-cause analysis of problems on process machinery (6x faster)
➜ Predict failures and avoid sudden and inefficient stoppages
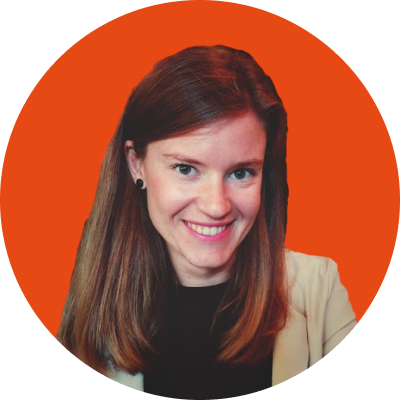
Get in touch with one of our experts
Martina Zanetti